Banner Image: © Parilov / Adobe Stock
October 2, 2023
I am writing this blogpost to bookend my first summer off work since high school. In this entry, I am going to talk about my many adventures, lessons learned, and completed/upcoming projects. This post coincides with the release of my new mega guide: Mastering CNC Plasma Cutting, so definitely checkout that video on YouTube if you haven’t already.
Finding Motivation in the Summer
As mentioned in my last post, I started a 9-month appointment teaching Digital Fabrication courses at Vanderbilt University. When the school year ended on May 4th, I woke up the next day with nothing to do. It was the strangest feeling – no meetings, no assignments to grade, and no emails to respond to. I couldn’t remember the last time my life was this quiet. Most professors, especially those on a teaching-track, instruct summer courses or advise undergraduates who are performing research during this time off. This is an optional but great way to fill the 3-month income gap. However, one of the reasons I was interested in a professorial career was the freedom to explore my own projects in the summer. After all, it was my personal projects that provided the foundation for the Digital Fabrication curriculum.
On May 5th, I went through my normal morning routine. At any minute I was expecting to feel a strong urge to go down to the garage and start working on my next project but that urge never came. Don’t get me wrong, mentally I wanted to get to work, but physically my body preferred to sit on the couch and watch Netflix or play video games. This wasn’t a feeling I was used to as my YouTube projects were normally a continuation of my week’s tasks. I was already in the habit of working, so I just kept working. I am sure that the urge to be a couch potato is a daily feeling that sole proprietors and entrepreneurs have to overcome, especially when you are only accountable to yourself. This was the first lesson that I learned over the summer: A routine of productivity is key.
Filament Extrusion Video
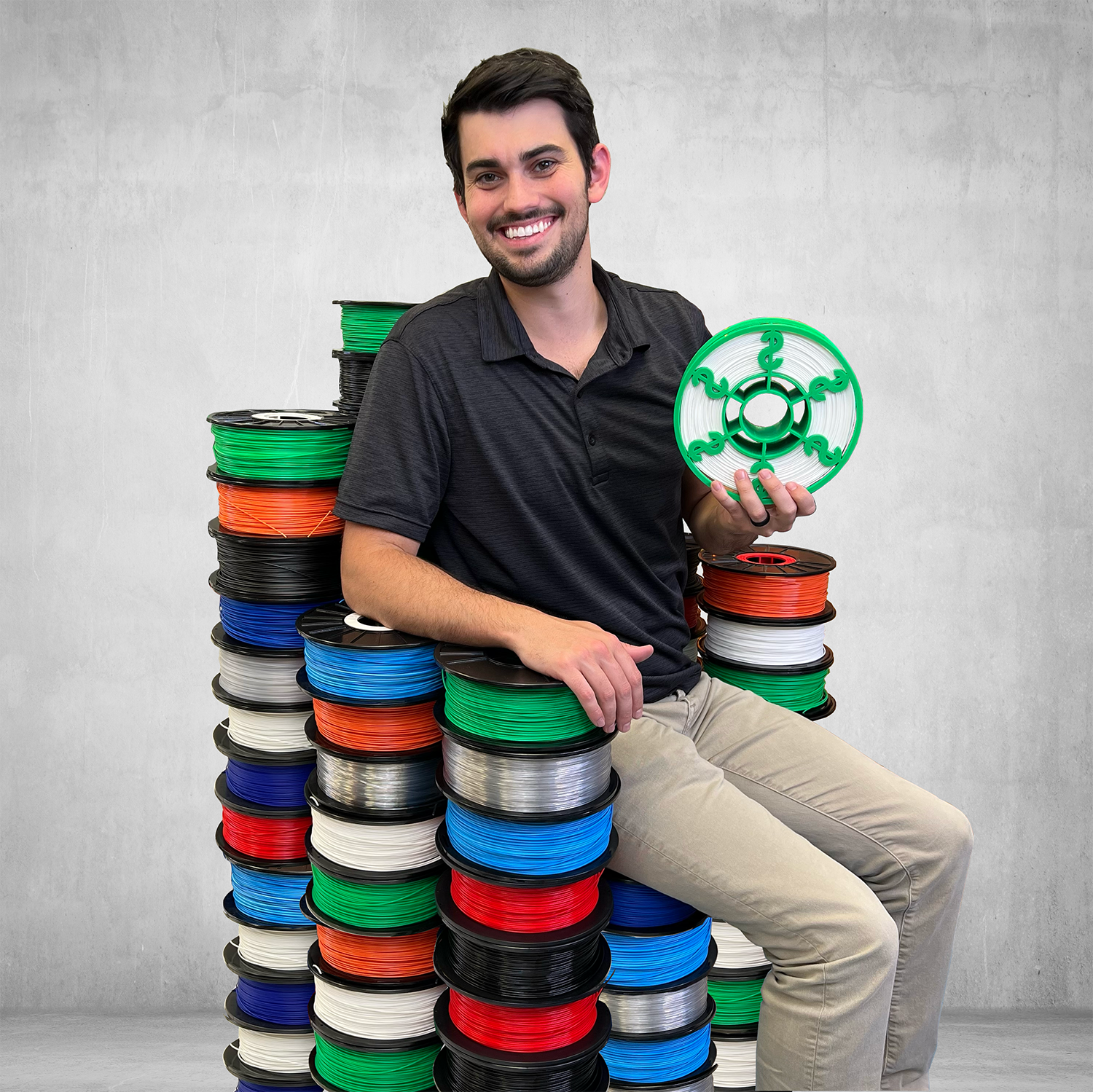
Once I was back in the groove, I started to plan the first video of the summer: How to Extrude 3D Printer Filament (Basics of Screw Extrusion). My video ideas always start with a device, whether it is a commercial product or a DIY design. I then write a script around how the components or technology within the device enable its function. For this video, I was supplied the EX6 extruder by Filabot. Screw extruders while made of relatively simple components (e.g., motors, screw, barrel, and heaters) rely on complex polymer rheology to uniformly melt and extrude a consistent filament. By far the most difficult part of planning a video is figuring out how to explain advanced topics without oversimplifying or going over viewer’s head. The point I was trying to drive home in the video is that a long screw, which features a special tapered geometry, is needed to sufficiently heat and mix the molten plastic to achieve a filament with little deviation from the desired 1.75 mm diameter. Longer screws are more difficult to manufacture and require more torque to turn (i.e., a larger motor is needed). These requirements are the reasons why low-cost filament extruders have not taken off at home because they simply do not have the right screw for the throughput or consistency to be economically viable. I have more information in my written extrusion guide, found here, if you are interested.
I was able to successfully extrude a variety of both neat and composite plastics, but from a viewership perspective this video underperformed with only about 50k views. However, it has the best like to dislike ratio out of any of my videos (~99.5%). This has put me in an interesting spot. Less people are watching but of the people who do, a greater percentage is finding the content useful. I observed a similar trend for my Mill Enclosure video as well. Of course, the way to reverse this trend would be to shorten my content by going into less detail and/or working on topics that are less niche. It’s so painstakingly obvious that shortform content is king. Not only is it easier to release more videos to remind your audience that you exist, but there is also a greater appetite for content that fills short lulls in the day.
CNC Plasma Cutting Mega Guide
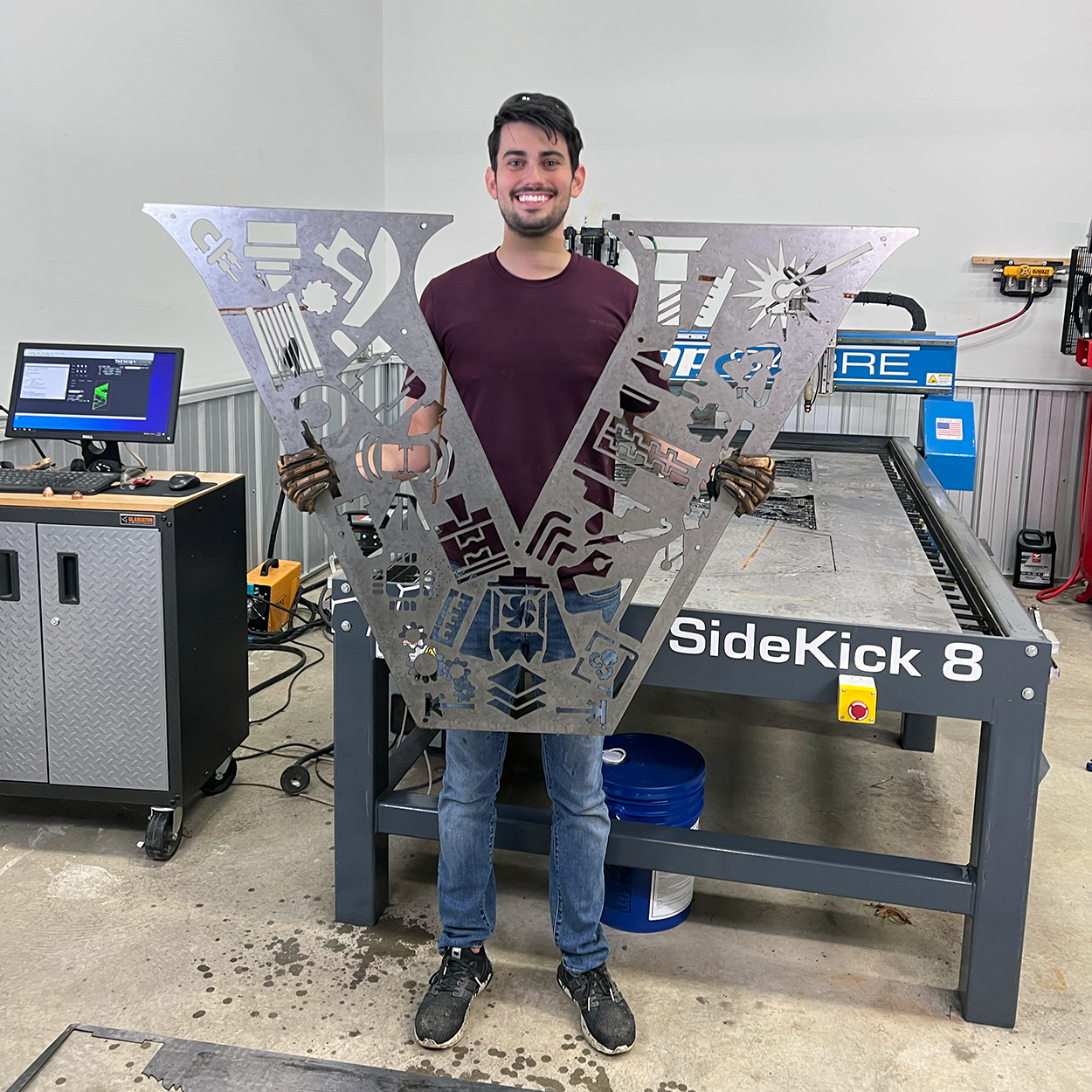
Instead of being sensible and working on shorter projects with widespread appeal, I doubled down on specialized, longform content by putting together a mega guide on CNC plasma cutting. This 1 hour and 40-minute video consumed most of my summer effort. With a 20,000-word script and hundreds of hours of video clips, I set out to explain every detail of the plasma cutting process from loading sheet metal on the table with a vacuum lifter to generating the digital toolpaths required to automatically move the torch along the perimeters of the desired parts. The depth of this guide rivals my How to Build a 3D Printer video but I was able to complete it in a third of time with my now open summer. I have no idea how this video will perform, but I have made a conscious decision to stick with my long, in-depth videos instead of pivoting to a more lucrative content style. I want my videos to be a textbook equivalent, serving as a resource for many years.
I was motivated to create this guide on CNC plasma cutting because I had several orders for my CNC Mill enclosure kits, some small signage projects, and firepits. I was cutting steel almost every day. None of these projects were notable enough to produce a video on, but I wanted to share how I run my plasma cutter to achieve dross-free cuts with low angularity. From a high-level, plasma cutting is easy to understand: a hot plasma melts and blows away the molten metal to separate the scrap metal from the final part. But when you zoom in, the technology and features that allow for the torch to perform hundreds of cuts without issue are more involved. With over 25 topics, this is a great video for introducing plasma cutting to the newcomer and some of the advanced tips are sure to even teach old dogs new tricks. The barrier to get into plasma cutting is the lowest it has ever been with fully equipped CNC tables only costing a couple thousand dollars. I have a written guide recommending features and plasma cutting units that you should be on the lookout for (read more here).
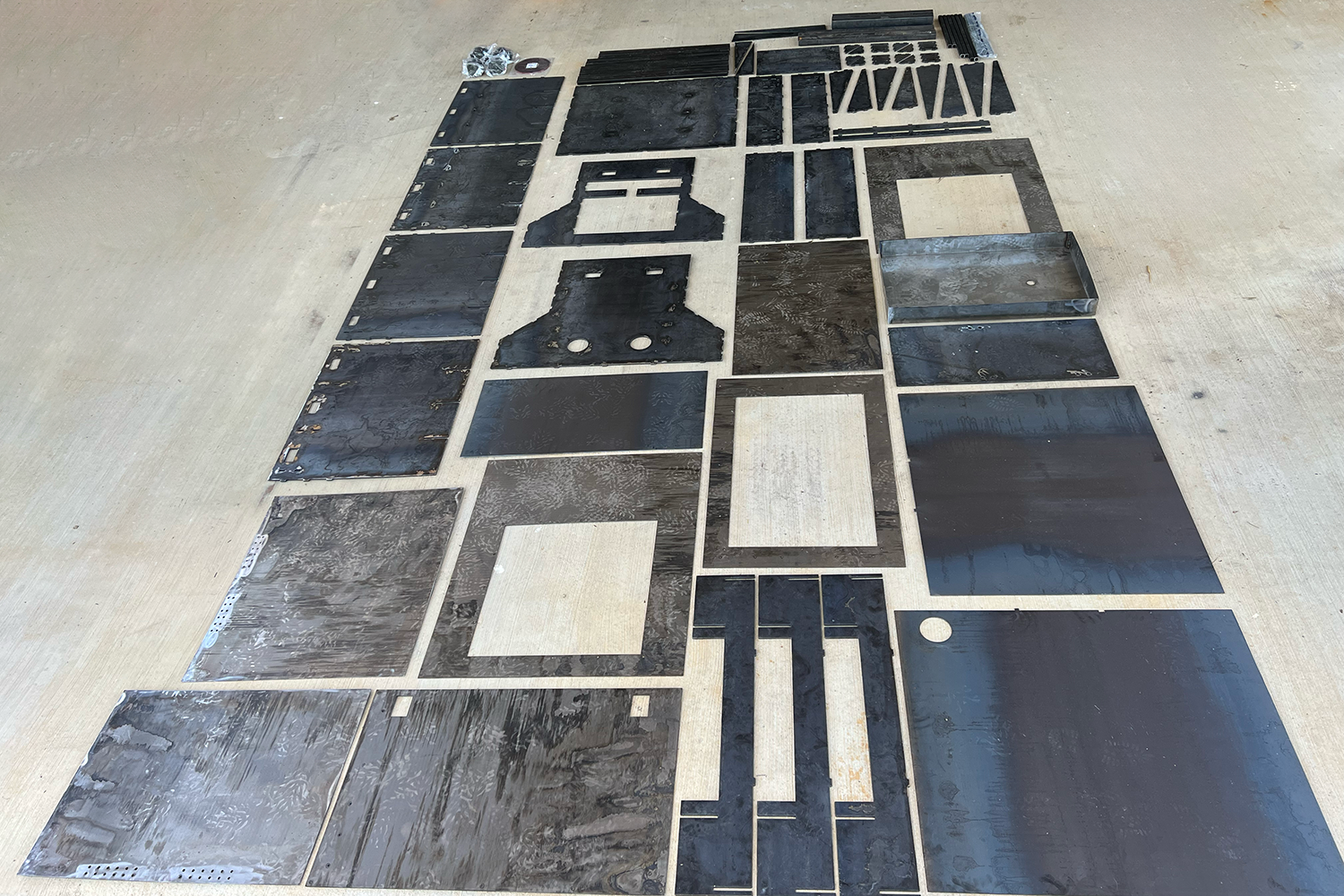
I truly believe that the depth and quality of information in this video could easily be a part of a paid masterclass. However, I've chosen to share it freely because as a teacher I have seen how impactful accessible knowledge can be. Further, I have also made the plans for building the DIY vacuum lifter seen in the video available on my website (see here). The vacuum lifter has significantly improved my quality of life. I no longer have to find an extra pair of hands to help me load thin sheets (<1/4” or 6 mm). While my cheap lifting magnets have enough strength to move thicker sheets, they can’t pick up a single sheet from a stack, which causes storage issues.
I only created two videos in the summer???
I get a lot of slack in the YouTube comments for my slow, irregular release schedule. This is a good rather than bad problem because it means my viewers care when I am not publishing content. Continuing this trend, there was a 3-month wait between the filament extrusion and plasma cutting videos during what should have been a summer purely focused on YouTube. But I would like to point out, that both of these videos could have been broken up into several. In fact, I could have made 10, 10-minute videos from the plasma cutter video. There are two reason I try not to split up my videos: 1) It holds me accountable. I can’t release the video until I finish recording everything I need to say from A-to-Z. If I released part 1 for a video, and there is low viewership, then honestly, I might not finish the series. 2) I don’t want this channel to become dominated by one CNC technology. If you are not interested in Plasma cutting, then you only have to skip one video. Your subscription feed will not be filled with a steady stream of plasma cutting content. I understand that there are drawbacks to this approach. Specifically, potential viewers may not want to watch a long video or may not know their answer is in the video due to the generic name (e.g., Mastering CNC Plasma Cutting). And of course, the slow release schedule coupled with seemingly disconnected video topics (e.g., going from plastic extrusion to plasma cutting) can give my viewers whiplash.
But the answer to this section title is: no! I was able to squeeze out a third video: Recycling Plastics into 3D Printer Filament. This is filmed and edited and will be released in a couple weeks. These three videos bring my total productivity if measured in content time to 3 hours for the summer, which I think it is pretty respectable for this largely being a one-man-band operation as Andi had to work.
Vacation
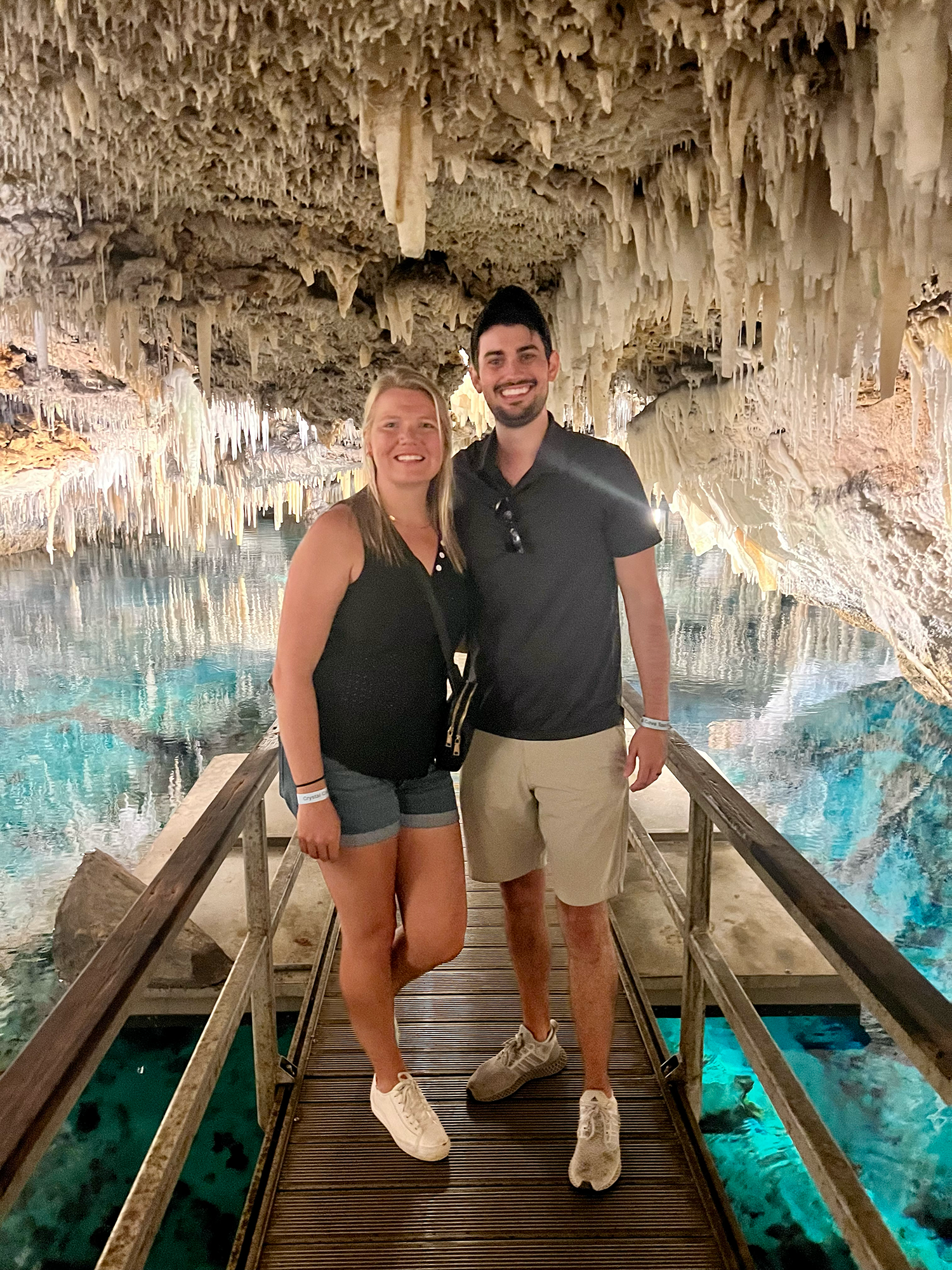
I didn’t just film videos all summer, but I had the opportunity to travel to several tropic islands for both a wedding and a family vacation. The summer started off with a trip to Sint Martin, a Caribbean Island, for Jeff’s wedding. Long time viewers may remember Jeff from the first couple Dr. D-Flo videos.
You can see all of Andi and I’s adventures on Sint Martin here.
And our favorite activities in Bermuda here.
I am writing this post with school is in full session, so I need to get back to grading and lecture planning. See you in the next one.
Dr. D-Flo
January 1, 2023
July 25, 2020
May 5, 2019
September 15, 2017